1976年,北京起重机械研究所研制出第一台AGV,建成第一套AGV滚珠加工演示系统,随后又研制出单向运行载重500公斤的AGV,双向运行载重500kg、1000kg、2000kg的AGV,开发研制了几套较简单的AGV应用系统。
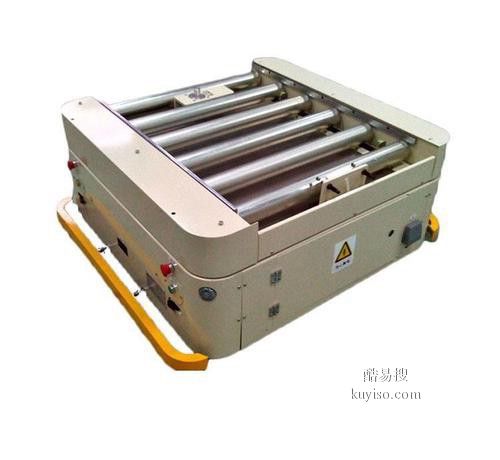
在国内AGV的技术来源有两种模式:一种是引进技术;一种是自有知识产权的技术。两种模式目前都涵盖AGV的所有技术,技术水平并无多大差别。引进技术主要是瑞典NDC的AGV控制系统技术,据了解NDC目前在国内现有3家合作伙伴。3
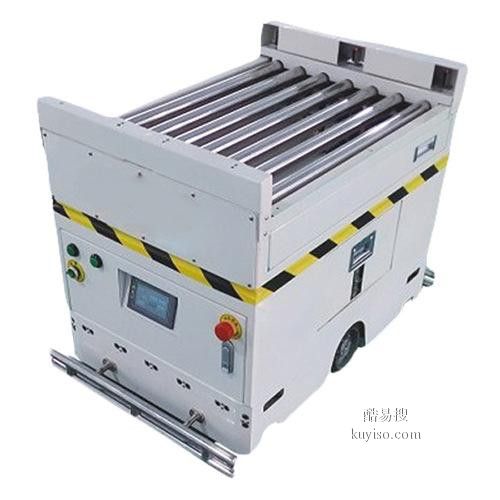
减速器、驱动器、控制与驱动电路等。驱动系统一般为闭环方式与开环方式,前者以伺服直流电机为主,后者以步进电机为主。
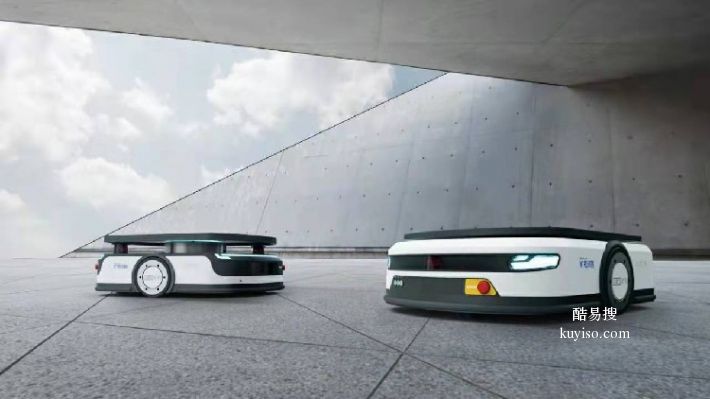
AGV即:AutomatedGuidedVehicle简称AGV,当前最常见的应用如:AGV搬运机器人或AGV小车,主要功用集中在自动物流搬转运,AGV搬运机器人是通过特殊地标导航自动将物品运输至指定地点,最常见的引导方式为磁条引导,激光引导,RFID引导等。磁条引导的方式是常用也是成本最低的方式,但是站点设置有一定的局限性以及对场地装修风格有一定影响;激光引导成本最高对场地要求也比较高所以一般不采用;RFID引导成本适中,其优点是引导精度高,站点设置更方便可满足最复杂的站点布局,对场所整体装修环境无影响,其次RFID高安全性稳定性也是磁条导航和激光导航方式不具备的。
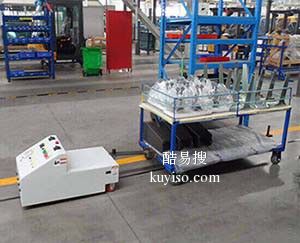
自动化程度高--由计算机,电控设备,磁气感应SENSOR,激光反射板等控制。当车间某一环节需要辅料时,由工作人员向计算机终端输入相关信息,计算机终端再将信息发送到中央控制室,由专业的技术人员向计算机发出指令,在电控设备的合作下,这一指令最终被AGV接受并执行--将辅料送至相应地点。
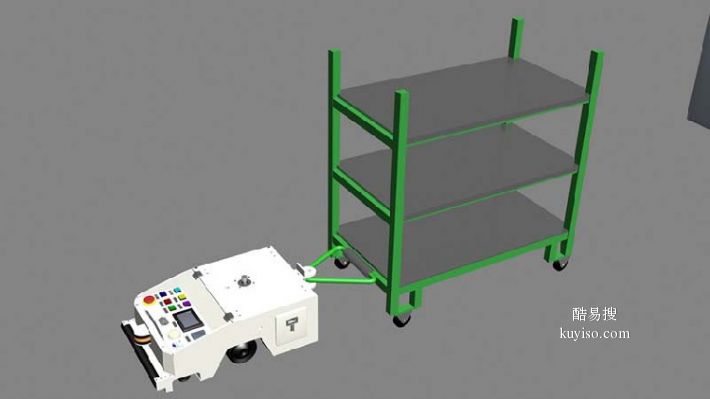
充电自动化--当AGV小车的电量即将耗尽时,它会向系统发出请求指令,请求充电(一般技术人员会事先设置好一个值),在系统允许后自动到充电的地方“排队”充电。另外,AGV小车的电池寿命很长(2年以上),并且每充电15分钟可工作4h左右。美观--提高观赏度,从而提高企业的形象。
4、安全性--人为驾驶的车辆,其行驶路径无法确知。而AGV的导引路径却是非常明确的,因此大大提高了安全性;
5、成本控制--AGV系统的资金投入是短期的,而员工的工资是长期的,还会随着通货膨胀而不断增加;
6、易维护--红外传感器和机械防撞可确保AGV免遭碰撞,降低故障率;
7、可预测性--AGV在行驶路径上遇到障碍物会自动停车,而人为驾驶的车辆因人的思想因素可能会判断有偏差;
8、降低产品损伤--可减少由于人工的不规范操作而造成的货物损坏;
9、改善物流管理--由于AGV系统内在的智能控制,能够让货物摆放更加有序,车间更加整洁;